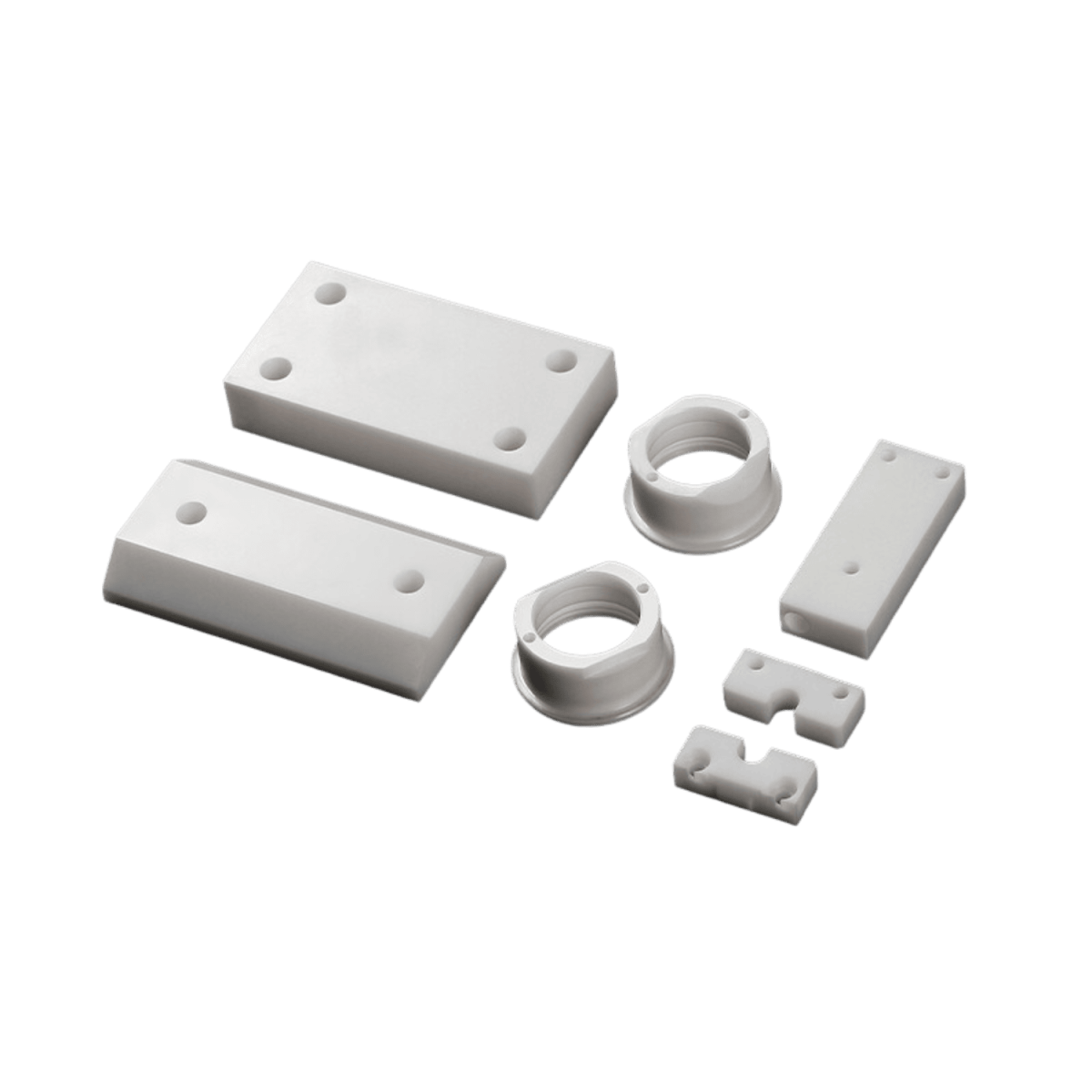
Al2O3 Alumina Ceramics
Alumina ceramic, also known as aluminum oxide ceramic, is a type of ceramic material made from aluminum oxide (Al2O3). It is a highly durable and wear-resistant material that is commonly used in a variety of industrial applications, including electronics, aerospace, automotive, and medical industries.
Details of Alumina Ceramics
What is alumina ceramic?
Alumina ceramic, also known as aluminum oxide ceramic, is a type of ceramic material made from aluminum oxide (Al2O3). It is a highly durable and wear-resistant material that is commonly used in a variety of industrial applications, including electronics, aerospace, automotive, and medical industries. Alumina ceramic is known for its high strength, hardness, and thermal stability, making it an ideal material for high-temperature and high-stress environments. It is also an excellent electrical insulator and has good corrosion resistance properties.
Alumina ceramic is available in various forms, including tiles, rods, tubes, and custom shapes, and can be manufactured using different processes such as dry pressing, extrusion, and injection molding.
Types of alumina ceramic
There are mainly four types of alumina ceramics:
- 96% Al2O3 ceramic: A type of ceramic material that is composed of 96% aluminum oxide (Al2O3) and 4% other materials. It has high mechanical strength, good wear resistance, and excellent electrical insulation properties. It is commonly used in applications such as electrical insulators, cutting tools, and wear-resistant components.
- 97% Al2O3 ceramic: A type of ceramic material that is composed of 97% aluminum oxide (Al2O3) and 3% other materials. It has similar properties to 96% alumina ceramic, but with slightly higher strength and hardness. It is commonly used in applications such as ball bearings, pump seals, and high-temperature furnace components.
- 99.7% Al2O3 ceramic: A type of ceramic material that is composed of 99.7% aluminum oxide (Al2O3) and 0.3% other materials. It has extremely high mechanical strength, excellent wear resistance, and good thermal shock resistance. It is commonly used in applications such as semiconductor processing equipment, medical implants, and high-temperature furnace components.
- Al2O3-ZrO2 ceramic: A type of ceramic material that is composed of a mixture of aluminum oxide (Al2O3) and zirconium oxide (ZrO2). It has high strength, toughness, and wear resistance, as well as good thermal shock resistance. It is commonly used in applications such as cutting tools, bearings, and dental implants.
Properties of alumina ceramic
Mian color of Al2O3 Ceramics are white and off-white.
Alumina ceramic parts are a high-performance material that offers several advantages over other materials. They are highly resistant to wear and corrosion, very hard and strong, and electrically insulating. Alumina ceramic parts are used in a wide range of applications, including electronics, aerospace, automotive, medical, and many others. Following is the property sheet:
Type | Unit | Test Standard | Alumina | |||
Material | Al₂O₃ 96% | Al₂O₃ 97% | Al₂O₃ 99.7% | Al₂O₃-ZrO₂ | ||
Colour | white, ivory | white, ivory | white, ivory | yellow | ||
Density | g/cm³ | ISO18754:2003 | 3.6 | 3.65 | 3.9 | 4.2 |
Flexural strength | Mpa | ASTM-C1161-13 | 310 | 360 | 400 | 500 |
Compressive Strength | Mpa | GB/T8489-2006 | 2200 | 2250 | 2450 | 2700 |
Modules of Elasticity (young) | Gpa | ASTM-C1198-09 | 300 | 330 | 380 | 350 |
Fracture Toughness | MPa*m1/2 | ASTM-C1421-18 | 3.5 | 3.5 | 4 | 3.5 |
Poision’s Ratio | ASTM-C1421-18 | 0.22 | 0.23 | 0.22 | 0.24 | |
Hardness HRA | HRA | RICKWELL 60N | 88 | 90 | 91 | 91 |
Vickers Hardness | HV1 | ASTM-C1327-15 | 1250 | 1450 | 1600 | 1600 |
Thermal Expansion Coefficient | 10-6K-1 | ASTM-E1461-13 | 7.2 | 7.1 | 6.8 | 9.2 |
Thermal Conductivity | W/mk | ASTM-E1461-13 | 24 | 25 | 32 | 8 |
Thermal Shock Resistance | △T.℃ | / | 200 | 200 | 220 | 470 |
Max Use Temperature in oxidizing Atmosphere | ℃ | NO LOAD CONDITION | 1000 | 1000 | 1200 | 1000 |
Max use Temperatur in reducing or Inert Atmosphere | ℃ | NO LOAD CONDITION | 1000 | 1000 | 1400 | 1000 |
Volume Resistivity at 20°C | Ωcm | / | 1014 | 1014 | 1015 | 1014 |
Dielectric Strength | kV/mm | / | 13 | 16 | 20 | 16.5 |
Dielectric Constant (1MHN) | ASTM-D2149-13 | 9.5 | 9.5 | 9.5 | 10 | |
Dielectric Loss Angle at 20C, 1MHz | tanδ | ASTM-D2149-13 | 3X10-4 | 3X10-4 | 1X10-4 | 2X10-4 |
Advantages of Alumina Ceramics
High hardness: Alumina ceramics are extremely hard and have a high resistance to wear and abrasion.
High strength: Alumina ceramics have high compressive strength, making them ideal for use in high-stress applications.
High temperature resistance: Alumina ceramics can withstand high temperatures without degrading or losing their properties.
Chemical resistance: Alumina ceramics are highly resistant to chemical attack, making them ideal for use in harsh chemical environments.
Electrical insulation: Alumina ceramics are excellent electrical insulators, making them ideal for use in electrical and electronic applications.
Biocompatibility: Alumina ceramics are biocompatible, meaning they can be used in medical applications without causing harm to the body.
Low thermal expansion: Alumina ceramics have a low coefficient of thermal expansion, meaning they do not expand or contract significantly with changes in temperature.
High stiffness: Alumina ceramics have a high modulus of elasticity, making them stiff and resistant to deformation.
Usages of Alumina Ceramics
Alumina ceramics are a type of structural ceramic product that is made from aluminum oxide (Al2O3). They are known for their high strength, hardness, and resistance to wear and corrosion. Here are some of the common usages of Alumina ceramics:
Electrical insulators: Alumina ceramics are excellent electrical insulators and are used in a variety of electrical applications, including high-voltage insulators, spark plugs, and electronic components.
Cutting tools: Alumina ceramics are extremely hard and wear-resistant, making them ideal for use in cutting tools such as knives, blades, and drill bits.
Wear-resistant components: Alumina ceramics are often used in applications where wear and corrosion resistance are critical, such as pump components, bearings, and valves.
Medical implants: Alumina ceramics are biocompatible and are used in medical implants such as hip and knee replacements.
High-temperature applications: Alumina ceramics can withstand high temperatures and are used in applications such as furnace linings, kiln components, and heat exchangers.
Aerospace and defense: Alumina ceramics are used in aerospace and defense applications such as armor plating, missile components, and engine parts.
Overall, Alumina ceramics are versatile and widely used in various industries due to their excellent mechanical, electrical, and thermal properties.
Provide ON-SITE GUIDANCE for orders over $300,000
Compared to steel, technical ceramics have the potential to significantly increase the lifespan of equipment and enhance product precision
The whole production processes of Alumina Ceramics
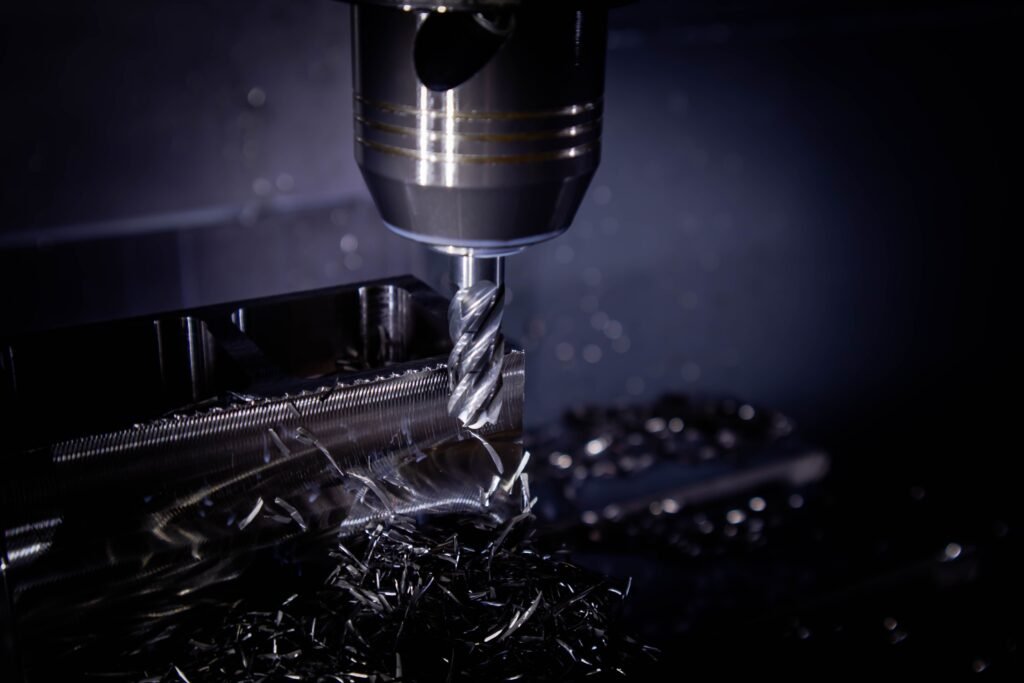
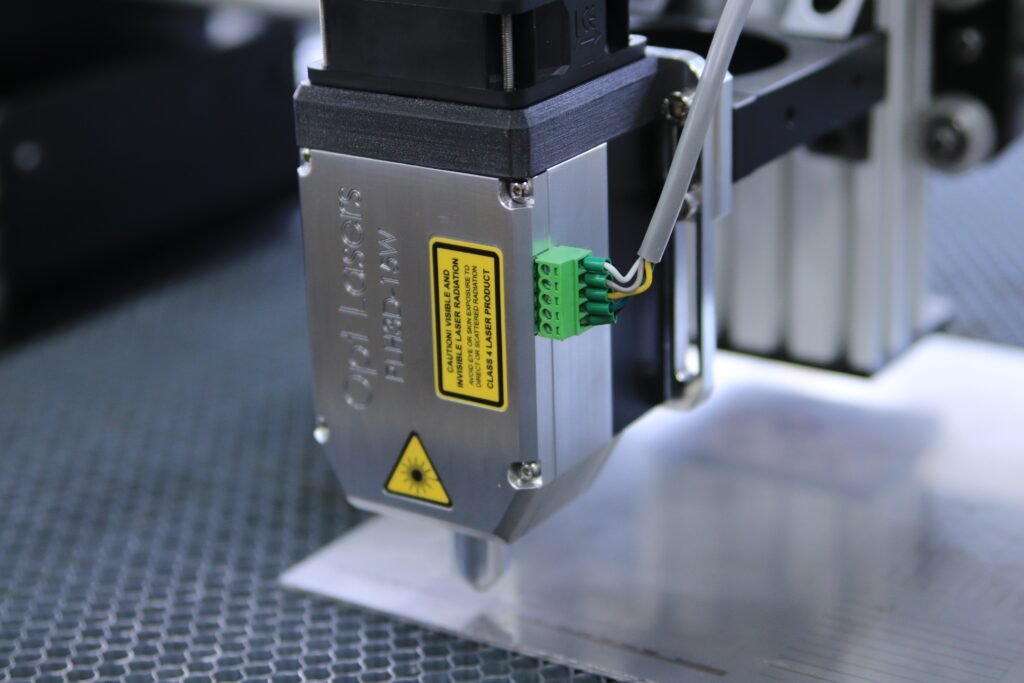
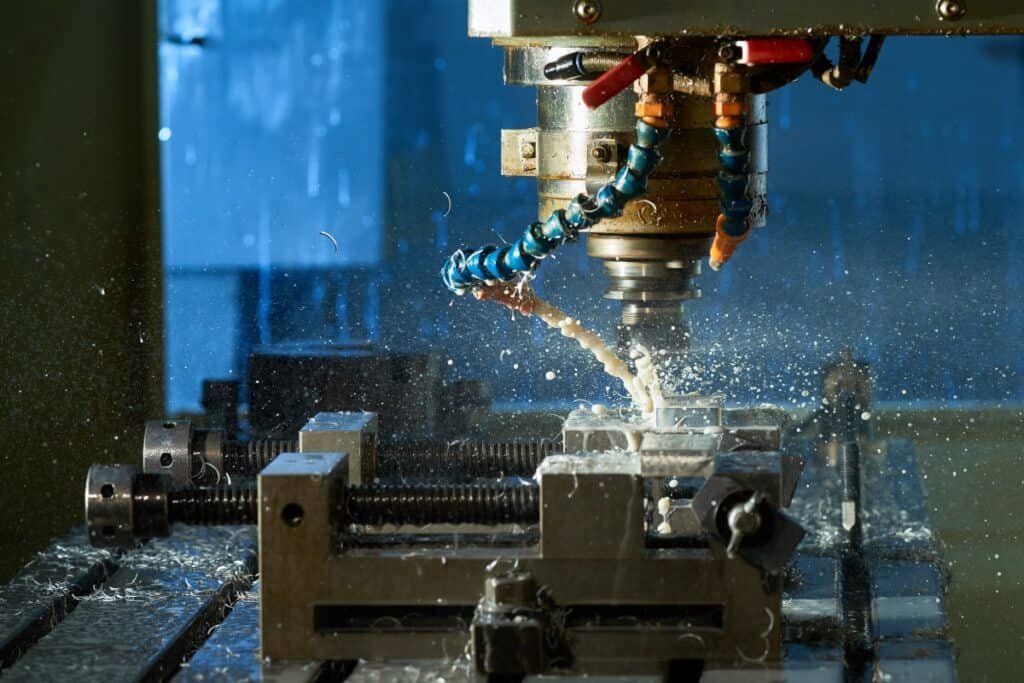
Shaping
Shaping the ceramic material into the desired form. This can be done using a variety of techniques, including extrusion, injection molding, or pressing. The shaped material is then dried to remove any excess moisture.
Firing
The shaped and dried material is then fired in a kiln at high temperatures (typically between 130°C and 170°C) to sinter the particles together and form a dense, hard ceramic material. The firing process can take several hours to several days, depending on the size and complexity of the part.
Finishing
After firing, the ceramic material may be finished by grinding, polishing, or other techniques to achieve the desired surface finish and dimensional accuracy.
Quality Control
Throughout the production process, the ceramic material is subjected to rigorous quality control measures to ensure that it meets the required specifications for strength, hardness, and other properties.
Is It Good As Metals? Things You Need To Know
To save you from worries, here are some facts you need to know about our structural ceramic parts supplies:
High Temperature Resistance
Advanced ceramics can withstand higher temperatures than most metals, making them ideal for use in high-temperature applications.
Hardness And Wear Resistance
Structural ceramics are much harder and more wear-resistant than metals, making them ideal for use in applications where wear and tear are a concern.
Corrosion Resistance
Ceramics are highly resistant to corrosion, making them ideal for use in harsh environments where metals would quickly corrode.
Electrical Insulation
Ceramics are excellent electrical insulators, making them ideal for use in electrical and electronic applications.
Biocompatibility
Some advanced ceramics are biocompatible, meaning they can be used in medical applications without causing harm to the body.
Lightweight
Ceramics are generally lighter than metals, making them ideal for use in applications where weight is a concern.
Low Thermal Expansion
Ceramics have a low coefficient of thermal expansion, meaning they do not expand or contract significantly with changes in temperature, making them ideal for use in precision applications.